Optical Coherence Tomography (OCT) in Laser Welding: Advancing Quality Control and ROI
- johnz54
- Dec 20, 2024
- 4 min read
Updated: Feb 4

In today’s manufacturing landscape, achieving consistent, high-quality laser welds while maintaining production efficiency isn’t just desirable—it’s essential for staying competitive. Optical Coherence Tomography (OCT) has emerged as a game-changing technology in this space, offering manufacturers unprecedented insight into laser welding process monitoring and control.
Let’s explore why manufacturers are increasingly investing in OCT technology and examine the compelling return on investment it offers.
Understanding OCT in Laser Welding
Optical Coherence Tomography technology uses low-coherence interferometry to provide high-resolution, cross-sectional imaging of weld processes in real-time. Think of it as an ultrasound for light—using light waves instead of sound waves to achieve far greater precision and detail.
This advanced technology allows manufacturers to monitor critical weld parameters in real-time, ensuring high-quality results. These parameters include:
Penetration depth: Ensures welds meet structural requirements with real-time laser weld depth measurement.
Keyhole formation and stability: Manages molten material flow to reduce defects.
Weld seam geometry: Maintains proper alignment and uniformity of welds for effective seam tracking in laser welding.
Surface defects: Identifies imperfections such as porosity, spatter, or roughness.
OCT is particularly valuable for non-destructive testing in medium- to high-volume laser welding applications, including automotive, aerospace, and electronics. Its ability to provide precise, real-time data enhances process control, reduces defects, and improves overall efficiency.
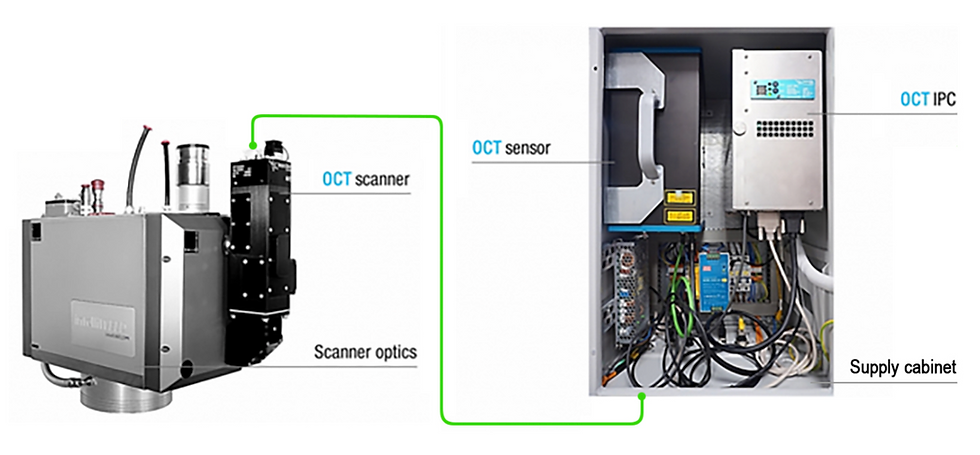
The Real ROI of OCT Implementation
The business case for OCT implementation is compelling when you consider both direct cost savings and indirect benefits:
Reduced Scrap and Rework: Traditional quality control methods often detect defects after they’ve occurred, leading to costly material waste and rework. OCT enables real-time laser welding process monitoring and immediate adjustments, significantly reducing scrap rates.
Minimized Destructive Testing: Implementing OCT capabilities can replace up to 70% of destructive testing methods in quality management workflows. This not only preserves valuable components but also accelerates testing cycles and reduces material costs.
Accelerated Production Speeds: With confidence in real-time quality monitoring, manufacturers can often increase welding speeds without compromising quality. Many facilities report 15-25% improvements in overall throughput after implementing OCT systems.
Labor Cost Optimization: By automating inspection processes that previously required manual oversight, OCT systems reduce labor costs while improving accuracy.
Quality Documentation and Traceability: OCT systems automatically generate comprehensive weld quality records, reducing documentation time and improving traceability. This is especially valuable in industries with strict regulatory requirements, saving up to 10 hours or more per week in quality assurance tasks.
Li10 and Lessmūller: A Partnership for Excellence in Laser Welding Process Monitoring
As the exclusive sales and service partner for Lessmūller Lasertechnik in North America, Li10 provides access to some of the most advanced OCT-based welding process monitoring sensor technologies on the market. Lessmūller’s OCT systems are designed specifically for seamless integration into modern laser welding monitoring systems, offering unique advantages such as:
Streamlined form factor: Compact designs that fit easily into a wide range of manufacturing setups.
High scanning rates: Enables real-time monitoring for superior process control and defect prevention.
Broad compatibility: Unlike most other OCT products, Lessmūller systems are compatible with most common laser optics, allowing easy implementation without the need for extensive system modifications.
Seamless integration: Effortlessly integrates with existing production systems, improving workflow and minimizing downtime.
Advanced analytics and reporting: Offers deep insights into laser weld depth measurement, seam tracking, and other critical parameters, all while automating documentation.
Proven reliability: Built to withstand demanding industrial environments for consistent performance.
By partnering with Lessmūller, Li10 delivers not only cutting-edge OCT technology but also expert support for system installation, process optimization, and ongoing maintenance. This ensures that manufacturers across North America can take full advantage of advanced laser welding monitoring systems to boost efficiency and quality.
Implementation Considerations for Seam Tracking and Laser Welding Monitoring Systems
A successful OCT implementation typically involves:
Thorough process analysis and requirements definition
Integration planning with existing production systems
Staff training and development of standard operating procedures
Establishing new quality control protocols
Regular system maintenance and calibration
When evaluating OCT solutions, manufacturers should consider factors such as production volume, material types, integration needs, and budget constraints. Choosing a robust solution like Lessmūller’s OCT systems, with their broad compatibility and high scanning rates, can simplify implementation and maximize ROI.
The Bottom Line
Based on industry data, manufacturers typically see full ROI on OCT investments within 12-18 months through combined savings from:
Reduced material waste
Decreased labor costs
Improved throughput
Reduced warranty claims
For most manufacturing operations, these improvements can translate to significant annual savings, making OCT implementation a compelling investment for quality-focused manufacturers.
Looking Ahead
The future of manufacturing lies in the adoption of Industry 4.0 technologies, and OCT is at the forefront of this revolution. Advanced laser welding monitoring systems, powered by OCT, are already helping early adopters achieve unprecedented levels of quality and efficiency. From improved seam tracking in laser welding to precise laser weld depth measurement, OCT is transforming quality control standards across industries and delivering substantial ROI.
At Li10, we’re proud to be the exclusive North American sales and service partner for Lessmüller Lasertechnik, offering industry-leading OCT systems and expert support. Whether you’re looking to enhance your welding monitoring sensor technologies or implement a cutting-edge laser welding process monitoring solution, our team is here to help.
Ready to learn more? Reach out to the laser welding experts at Li10 today and discover how OCT weld monitoring technology can transform your manufacturing operations.